PP板材成型过程及模具温度对其收缩率的影响
一、PP板材的成型过程
PP(聚丙烯)板材的成型工艺主要包括挤出成型和模压成型两种主流方式,其中挤出成型因效率较高、适合***规模生产而被广泛采用。以下是其详细流程:
1. 原料准备与预处理
主要原料:以聚丙烯树脂为基础,根据需求添加抗氧化剂、光稳定剂、抗静电剂、增韧剂等助剂,以提升耐热性、抗老化性或***定功能。
干燥处理:聚丙烯颗粒需经过70100℃的预热干燥(时间24小时),以去除水分,防止熔融过程中产生气泡或降解。
配料混合:通过搅拌设备将树脂与助剂均匀混合,确保板材性能的均一性。
2. 熔融挤出
加热塑化:干燥后的原料进入挤出机,在180240℃的高温下熔化,螺杆设计需适配PP的流变***性,以确保熔体流动性和温度均匀性。
螺杆作用:螺杆的剪切力促进物料塑化,同时推动熔融态PP通过模具定型。
3. 模具成型与冷却定型
模具设计:模具形状决定板材的厚度和宽度,内部通常配置冷却通道以加速固化。模具温度是影响收缩率的关键因素之一。
冷却固化:挤出的板材通过冷却辊或空气冷却快速定型,均匀冷却可减少内应力,提升尺寸稳定性。
4. 牵引与切割
牵引定型:冷却后的板材经牵引设备拉直,确保平整度和尺寸精度。
切割加工:根据需求切割成***定长度,后续可能进行钻孔、打磨或涂装等处理。
5. 品质检验与包装
检验标准:包括尺寸精度、外观质量、物理性能(如抗冲击性、耐化学性)等。
包装储存:防划伤、防变形包装,避免长期高温暴露以延缓老化。
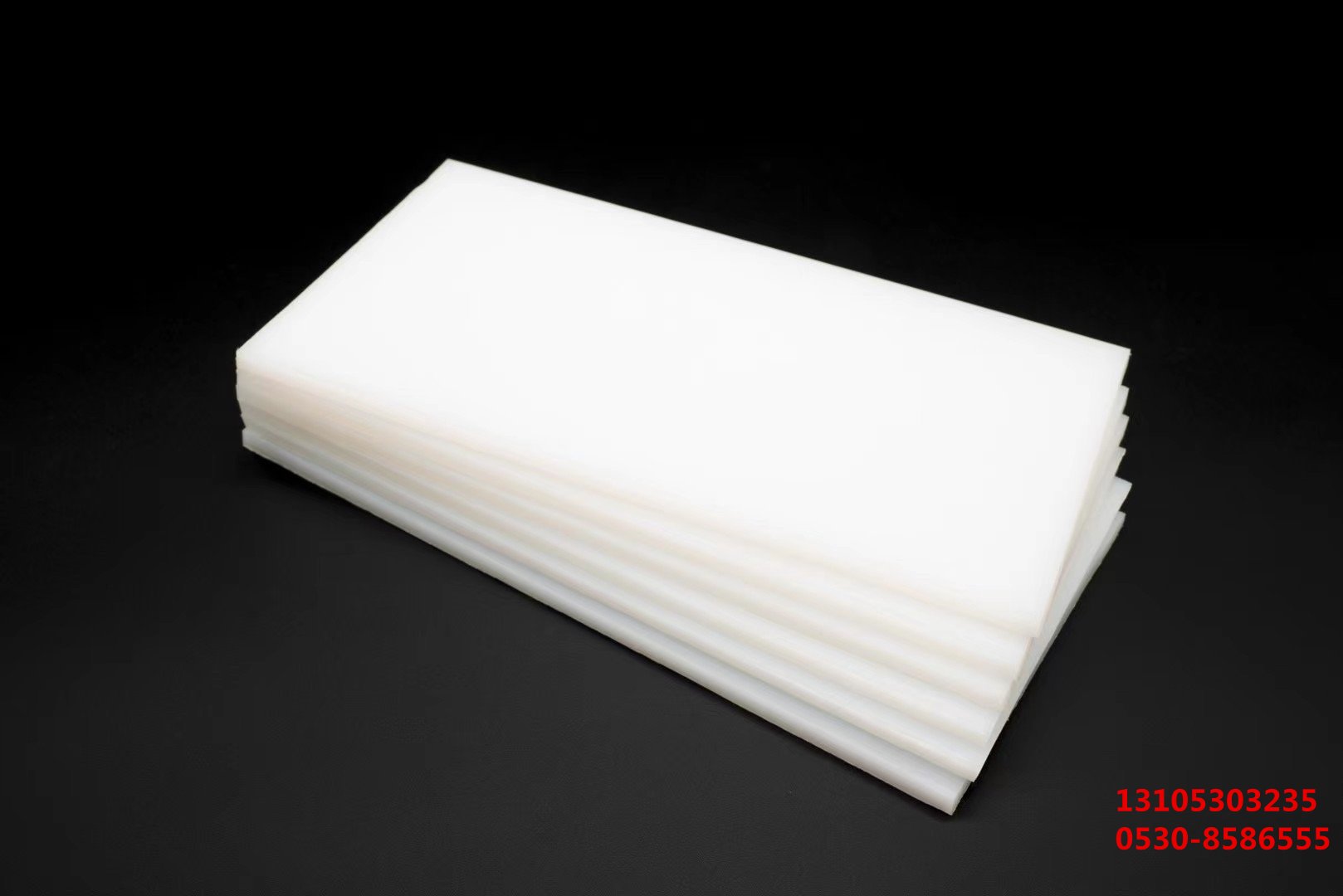
二、模具温度对PP板材收缩率的影响
模具温度是调控PP板材收缩率的核心参数之一,主要通过以下机制影响收缩率:
1. 结晶度与体积收缩
PP作为半结晶性聚合物,冷却过程中分子链会规则排列形成晶体,导致体积收缩。模具温度越高,PP的结晶度越高,收缩率随之增***。
数据参考:模具温度从40℃升至80℃时,PP制品的总收缩率可能增加0.5%1%。
2. 热膨胀与弹性压缩
模具温度升高会加剧制品的热膨胀效应,但同时也因冷却速度减缓导致弹性压缩作用减弱。综合作用下,模内收缩率可能小幅下降,但总收缩率(包括后收缩)仍随模温升高而上升。
3. 取向效应
高模温会加速分子链的解取向,降低因流动取向产生的收缩率差异,使收缩方向更均匀。
三、实际应用中的建议
1. 模具温度控制范围
一般推荐模具温度为4080℃,具体需根据板材厚度和性能需求调整。例如,薄壁或复杂结构板材可适当提高模温以减少应力。
2. 收缩率补偿策略
设计模具时需预留收缩余量,通常PP板材的收缩率范围为1.6%2.5%,高模温环境下可接近上限值。
加入玻璃纤维等填料可显著降低收缩率(如30%玻纤填充可使收缩率降至0.7%),但可能牺牲部分韧性。
3. 冷却系统***化
高效冷却可缩短成型周期,但需避免温差过***导致变形。建议采用分区控温或动态冷却技术。
综上所述,PP板材的成型过程需严格把控原料、温度、冷却等环节,而模具温度作为关键参数,需在收缩率控制与生产效率之间寻求平衡。在实际生产中,建议结合具体材料牌号和制品要求,通过试验***化工艺参数,以实现高精度成型。