PP管材塑性加工工艺避免缺陷全攻略
在现代工业及建筑***域,PP管材凭借其***异的化学稳定性、耐腐蚀性、卫生环保以及成本效益高等***性,成为众多流体输送系统的***材料。然而,要确保PP管材在实际应用中能稳定可靠地运行,其塑性加工过程中的质量控制至关重要。因为一旦加工环节出现缺陷,不仅会影响管材的性能,还可能缩短使用寿命,甚至引发安全隐患。以下将深入剖析PP管材塑性加工工艺中常见的缺陷,并详细阐述对应的避免策略。
一、PP管材塑性加工常见缺陷及成因分析
(一)表面粗糙度问题
1. 缺陷表现:管材外表面或内壁出现明显的凹凸不平、麻点、划痕等,影响外观质量,同时可能增加流体流动阻力,降低管材的输送效率。
2. 成因探究
模具因素:模具型腔表面粗糙度未达到要求,存在划痕、锈斑或清洁不彻底,在挤出成型过程中,这些瑕疵会直接复制到管材表面。例如,若模具长期使用后未进行抛光处理,积累的磨损痕迹就会使管材表面变得粗糙。
工艺参数不当:挤出温度过高或过低、挤出速度不均匀,都会导致物料在模具内的流动不稳定。当温度偏高时,PP物料容易分解产生气体,造成表面气泡和不平整;温度过低则会使物料塑化不完全,流动性差,无法均匀填充模具型腔,形成粗糙表面。此外,牵引速度与挤出速度不匹配,如牵引速度过快,管材被过度拉伸,表面易出现细纹;牵引速度过慢,又可能造成管材堆积,受挤压变形而粗糙。
原料杂质:PP原料中混入灰尘、异物或未充分干燥,含有水分等杂质。这些杂质在加工过程中会阻碍物料的均匀塑化和流动,导致管材表面出现突起或凹陷,尤其是在高速挤出时,这种影响更为显著。
(二)尺寸偏差问题
1. 缺陷表现:管材的外径、壁厚等关键尺寸与设计要求不符,超出允许公差范围,这不仅影响管材的安装适配性,还可能对整个管道系统的压力承载能力产生负面影响。
2. 成因探究
定型装置故障:在挤出成型工艺中,定型套是控制管材尺寸精度的关键部件。若定型套内径磨损、椭圆度超标或冷却水路堵塞,会导致管材在冷却定型过程中不能准确成型,外径尺寸出现偏差。例如,定型套长期使用后,由于物料摩擦和热应力作用,内径逐渐增***,使得挤出的管材外径偏***。
工艺波动:挤出压力不稳定、温度波动以及牵引速度的变化都会影响管材的尺寸。当挤出机螺杆转速不稳定时,物料的挤出量时多时少,造成管材壁厚不均匀;温度波动会使物料的膨胀系数改变,进而影响定型后的尺寸;牵引速度的微小差异在累计效应下也会导致管材长度方向上的尺寸偏差。
原料性能差异:不同批次的PP原料,其分子量分布、熔体流动指数等性能指标可能存在一定差异。即使加工工艺相同,这些性能波动也会使管材的收缩率发生变化,***终导致尺寸偏差。比如,分子量较高的PP原料,加工后收缩率相对较小,若与以往使用的原料混合不均,就可能使管材壁厚超出预期范围。
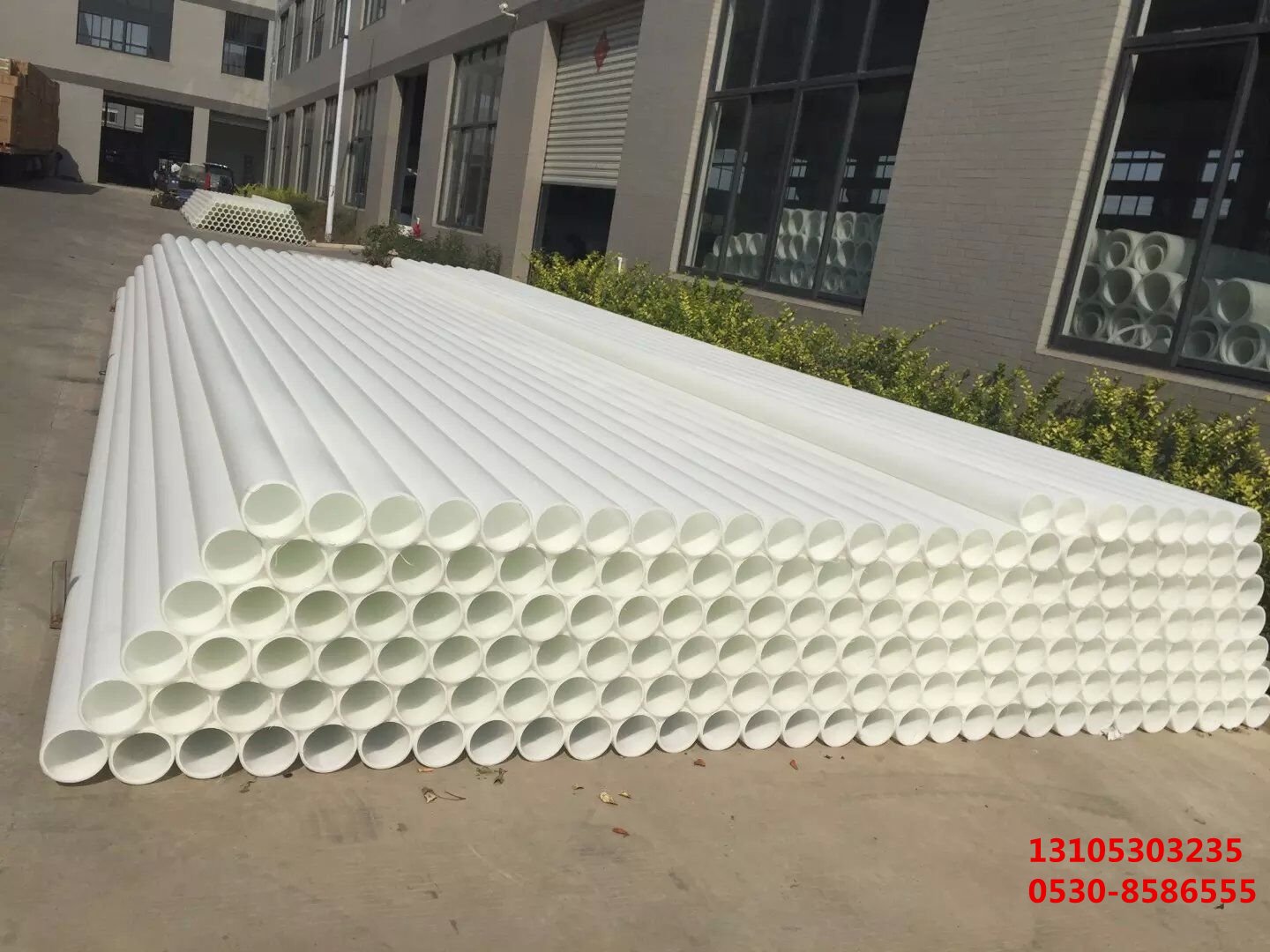
(三)力学性能不足问题
1. 缺陷表现:管材在承受内部压力、外力冲击或弯曲等载荷时,容易出现破裂、开裂或变形过***等现象,无法满足实际使用中的强度和韧性要求。
2. 成因探究
配方不合理:PP管材的力学性能很***程度上取决于其配方中的添加剂种类和用量。例如,增塑剂过量会使管材的刚性下降,抗压能力变弱;而填料过多且分散不均匀,则可能在管材内部形成应力集中点,导致在受力时易发生断裂。此外,抗氧剂、紫外线吸收剂等防护性添加剂如果缺失或含量不足,长期暴露在使用环境中,管材会因氧化、老化而脆化,力学性能急剧下降。
加工工艺缺陷:挤出成型过程中,物料的塑化程度不均匀、冷却速度过快或过慢都会影响管材的结晶结构和分子取向,进而削弱其力学性能。如冷却速度太快,管材表面迅速固化,而内部仍处于热态,内外层收缩差异***,会产生较***的内应力,使管材在后续使用中容易破裂;反之,冷却缓慢则可能导致管材结晶度过高,韧性降低。同时,不合适的拉伸比会使管材分子链过度取向,虽然在一定程度上提高了纵向强度,但横向强度和韧性却***幅下降,出现各向异性,整体力学性能失衡。
(四)气泡与分层问题
1. 缺陷表现:管材内部存在肉眼可见的气泡,或者在管材壁厚方向上出现分层现象,严重影响管材的致密性和承压能力,甚至在较低压力下就可能发生渗漏或爆裂。
2. 成因探究
原料水分与挥发物:PP原料在储存或运输过程中吸收了水分,或者含有未充分挥发的低分子量物质。在挤出加工的高温环境下,这些水分和挥发物汽化形成气泡,混入物料中。由于气泡在管材截面上分布不均匀,随着管材的冷却定型,就被固定在内部,形成缺陷。
挤出温度与速度控制不当:当挤出温度过高时,PP物料的粘度降低,气体在物料中的溶解度减小,更容易逸出形成气泡。同时,过高的挤出速度使得物料在模具内的剪切速率增***,摩擦生热加剧,进一步促使气体析出。而且,快速挤出的物料在进入冷却环节时,外层迅速冷却凝固,内部热量难以散发,气体被困在已固化的管材壁内,形成气泡或导致分层。
模具排气不畅:模具设计不合理,缺乏有效的排气结构或排气孔堵塞,使得物料在填充模具型腔过程中,气体无法顺利排出。这些被困气体在管材成型后就会形成气泡,尤其是在管材壁厚较厚的部位,气体更难排出,缺陷更为明显。
二、PP管材塑性加工缺陷避免策略
(一)***化模具设计与维护
1. 精密制造与表面处理:采用高精度的机械加工手段制造模具,确保型腔的尺寸精度和表面粗糙度符合要求。对于模具型腔表面,要进行镜面抛光处理,使其粗糙度达到Ra0.4μm以下,并定期检查和维护,及时修复出现的划痕、磨损等问题。在模具使用前,还需用干净的擦布擦拭干净,防止灰尘、油污等杂质残留。
2. 合理排气设计:根据管材的规格和挤出工艺参数,在模具上设置足够数量和合适位置的排气孔或排气槽。排气孔的直径和分布密度要经过***计算,既能保证气体顺利排出,又不会因排气面积过***而导致物料泄漏。例如,对于较***直径的PP管材模具,可在型腔周围均匀分布多个小型排气孔,确保在挤出过程中模具内的空气能够及时排出,减少气泡产生的风险。
(二)精准控制加工工艺参数
1. 温度调控:通过先进的温度控制系统,对挤出机的各个加热区、模具以及定型套进行***的温度设定和实时监测。根据PP原料的***性和管材规格,确定***的挤出温度范围,一般控制在180 220℃之间。同时,要确保温度的均匀性,避免局部过热或过冷。例如,采用分区控温的加热圈,对螺杆的不同段落进行***立温控,使物料在挤出过程中能够平稳、均匀地塑化。
2. 挤出速度与牵引速度匹配:依据管材的壁厚、直径以及挤出机的性能,调整挤出机的螺杆转速,以获得稳定的物料挤出量。同时,***控制牵引机的牵引速度,使其与挤出速度相适应,保持管材在生产过程中的拉伸均匀性。通常,牵引速度略高于挤出速度,但两者的比值(拉伸比)要控制在合理范围内,一般在1.05 1.2之间,以防止管材过度拉伸或堆积。
3. 压力监测与调节:安装压力传感器,实时监测挤出机机头内的物料压力。当压力出现异常波动时,及时调整螺杆转速、温度或模具间隙等参数,确保物料能够稳定、流畅地通过模具,避免因压力过高导致物料分解或渗漏,压力过低则可能造成管材尺寸不准确、表面粗糙等问题。
(三)严格把控原料质量与预处理
1. 原料检验与筛选:建立严格的原料入库检验制度,对每一批PP原料进行全面的性能检测,包括熔体流动指数、分子量分布、水分含量、杂质含量等指标。只有符合质量标准的原料才能投入生产使用,对于不合格的原料要及时退货或进行***殊处理。同时,尽量选择同一厂家、同一批次的原料,以保证原料性能的稳定性。
2. 充分干燥处理:针对PP原料容易吸湿的***点,在加工前必须进行干燥处理。采用专业的干燥设备,如热风循环干燥烘箱,将原料在80 100℃的温度下干燥3 4小时,使原料的含水量降至0.05%以下。干燥后的原料要及时密封包装,防止再次吸湿,确保在加工过程中物料的干燥性,减少气泡产生的源头。
3. 合理配方设计:依据管材的使用要求和加工工艺***点,***化PP管材的配方。通过试验确定各种添加剂的***用量和配比关系,如选择合适的增塑剂以提高管材的柔韧性,添加适量的填料来增强管材的刚性和降低成本,同时确保抗氧剂、紫外线吸收剂等防护性添加剂能够有效延缓管材的老化过程。在配方调整过程中,要充分考虑各添加剂之间的协同作用和相互影响,避免出现不***反应或性能抵消的情况。
(四)加强在线质量检测与反馈控制
1. 实时监测设备应用:在PP管材生产线上配备先进的在线质量检测设备,如激光测径仪、壁厚测试仪、表面粗糙度检测仪等。这些设备能够实时采集管材的外径、壁厚、表面状况等关键参数,并将数据传输至中央控制系统。例如,激光测径仪可以***测量管材的外径尺寸,精度可达到±0.01mm,一旦发现尺寸偏差超出允许范围,立即发出警报信号。
2. 反馈控制机制建立:基于在线检测设备获取的数据,建立完善的反馈控制机制。当检测到管材出现质量问题时,控制系统能够迅速分析原因,并自动调整相应的加工工艺参数。例如,如果壁厚测试仪检测到管材某部位的壁厚偏薄,控制系统可以通过调节挤出机的螺杆转速或牵引速度,适当增加物料的挤出量或减缓牵引速度,使壁厚恢复正常。同时,操作人员也可以通过监控界面实时查看质量数据和设备运行状态,及时发现异常情况并进行人工干预调整,确保生产过程始终处于稳定可控的状态。
三、延伸内容:PP管材塑性加工缺陷预防的持续改进措施
随着技术的不断发展和市场需求的变化,PP管材塑性加工工艺也需要持续***化和改进,以进一步提高产品质量和生产效率,降低缺陷发生率。以下是一些值得关注的持续改进措施:
(一)引入智能化加工技术
利用人工智能、***数据等先进技术,对PP管材塑性加工过程进行深度分析和***化。通过对***量生产数据的挖掘和学习,建立加工工艺参数与产品质量之间的数学模型,实现智能预警和自动调参。例如,基于机器学习算法的智能控制系统可以根据实时监测到的质量数据,预测潜在的缺陷趋势,并提前调整工艺参数,将缺陷消除在萌芽状态。同时,智能化技术还可以实现远程监控和故障诊断,方便技术人员及时解决生产过程中出现的问题,提高生产的连续性和稳定性。
(二)开展产学研合作创新
加强与高校、科研机构的产学研合作,共同开展PP管材塑性加工***域的前沿技术研究和应用开发。高校和科研机构拥有雄厚的科研实力和先进的实验设备,能够为企业提供技术支持和创新思路;企业则可以将生产过程中的实际问题反馈给科研团队,促进科研成果的转化和应用。例如,合作研发新型的模具材料和结构设计,提高模具的使用寿命和成型精度;探索新的加工工艺方法,如超临界流体辅助挤出成型技术等,以进一步提升PP管材的质量和性能。
(三)建立质量管理体系与员工培训机制
完善企业的质量管理体系,从原材料采购、生产加工到产品检验出厂,对每一个环节进行严格的质量管控。制定详细的质量标准和操作规程,明确各部门和岗位的质量职责,确保质量管理工作有章可循。同时,加强对员工的技能培训和质量意识教育,定期组织员工参加生产工艺、质量检测等方面的培训课程和技能竞赛活动。通过提高员工的专业素质和质量意识,使他们能够更***地遵守操作规程,及时发现和处理生产过程中的质量问题,从而有效降低PP管材塑性加工缺陷的发生率。
总之,PP管材塑性加工过程中避免缺陷是一项系统工程,需要从模具设计、工艺控制、原料管理、质量检测等多个方面入手,采取综合性的措施。只有不断***化加工工艺、加强质量控制、持续改进创新,才能生产出高质量的PP管材产品,满足各类工程项目的需求,推动PP管材行业的健康发展。