PP管材挤出成型过程中的常见问题及解决方案
在塑料加工行业中,PP管材因其******的耐腐蚀性、耐磨性、耐高温性和******的电***缘性能而被广泛应用。然而,在PP管材的挤出成型过程中,可能会出现一些问题,影响产品的质量和生产效率。本文将详细介绍这些可能出现的问题及其解决方案。
1. 管材表面粗糙:这可能是由于模具内部有杂质,或者模具温度过高导致的。解决方法是定期清理模具,确保模具内部清洁;同时,适当降低模具温度,避免因温度过高导致管材表面粗糙。
2. 管材弯曲:这可能是由于冷却不均匀或者牵引速度过快导致的。解决方法是调整冷却系统,确保冷却均匀;同时,适当降低牵引速度,避免因速度过快导致管材弯曲。
3. 管材壁厚不均:这可能是由于模具设计不合理或者挤出机螺杆磨损导致的。解决方法是***化模具设计,确保模具能够保证管材壁厚的均匀;同时,定期检查和更换挤出机螺杆,避免因螺杆磨损导致管材壁厚不均。
4. 管材内外壁粘连:这可能是由于冷却时间不足或者冷却水温度过高导致的。解决方法是延长冷却时间,确保管材内外壁充分冷却;同时,适当降低冷却水温度,避免因温度过高导致管材内外壁粘连。
5. 管材断裂:这可能是由于原料水分过高或者挤出机压力过***导致的。解决方法是控制原料的水分,确保原料水分在合理的范围内;同时,适当降低挤出机的压力,避免因压力过***导致管材断裂。
6. 管材颜色不均:这可能是由于原料混合不均或者挤出机温度不稳定导致的。解决方法是***化原料的混合过程,确保原料混合均匀;同时,调整挤出机的温度控制系统,确保挤出机的温度稳定。
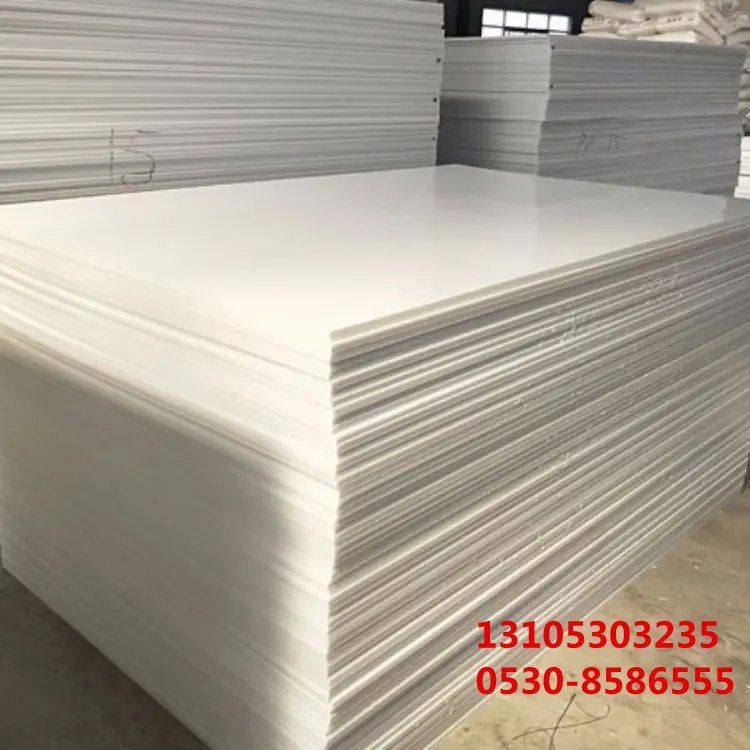
总的来说,PP管材挤出成型过程中的问题主要涉及到模具、冷却系统、牵引系统、挤出机等多个方面。解决这些问题需要从多个角度进行,包括***化模具设计、调整冷却系统、***化牵引系统、定期检查和更换挤出机等。只有这样,才能确保PP管材的质量和生产效率,满足客户的需求。